Frumecar Quality From Bay-Lynx
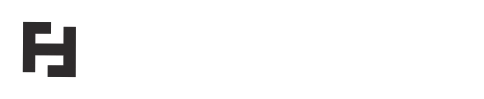
DRUM MIXER SOLUTIONS BUILT WITH YOU IN MIND
Our range of concrete drum mixers are designed with a clear commitment to enhancing mix consistency during operation, and ensuring safer driving and handling. With simple operation when pouring concrete, and optimising loading and unloading times, we ensure your operation runs efficiently. These are the high standards that we set for ourselves and our equipment.
In addition to their quality, it is essential to bear in mind that the standard equipment on Frumecar’s concrete mixers is of the highest level compared to the rest of the market, giving you more for your investment.
Their mixers have various features, including an anti-wear lining for the chute, a 6mm reinforcement plate on the drum blades, a hand trapping prevention system between the chutes, two storage cases for fire extinguishers, a second water connection, and auxiliary polyethylene chutes.
Built To Last
Frumecar’s concrete mixers are designed for optimal performance and many years of trouble free operation. All components and materials are sourced from leading suppliers. Built with High-quality SSAB steel “HARDOX” and “STRENX” grade.
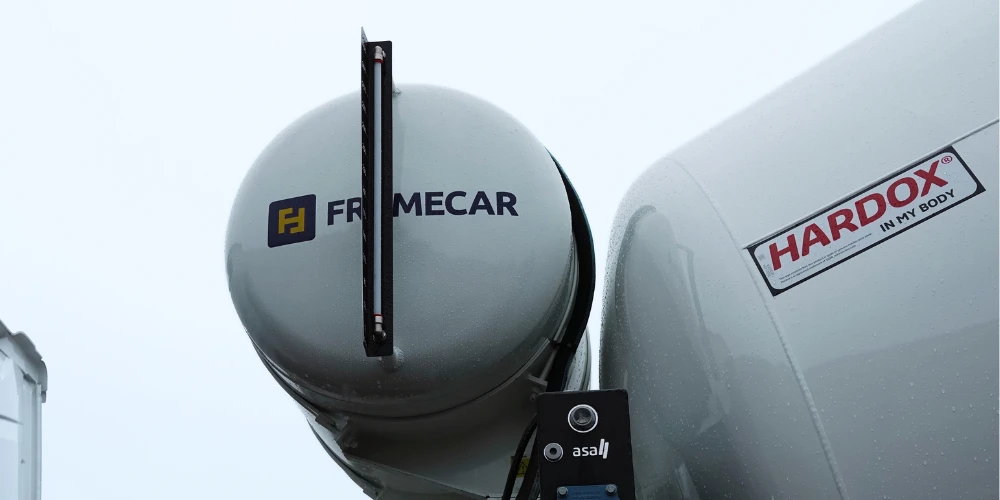
Designed To Perform
Every Frumecar mixer is designed to meet all your needs and simplify your work experience. They are built for continuous operation, ensuring hassle-free use with minimal maintenance effort. The materials, design, and components all focus on achieving this aim.
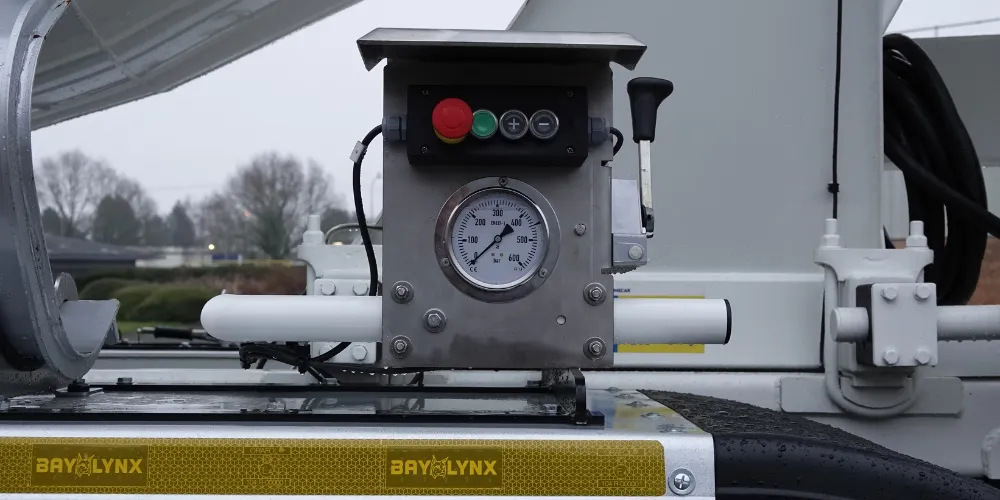
Easy To Maintain
Frumecar’s concrete mixers are designed to simplify your life. They feature easy access to all components, making maintenance straightforward and efficient. You can complete maintenance tasks quickly and with minimal effort with user-friendly elements.
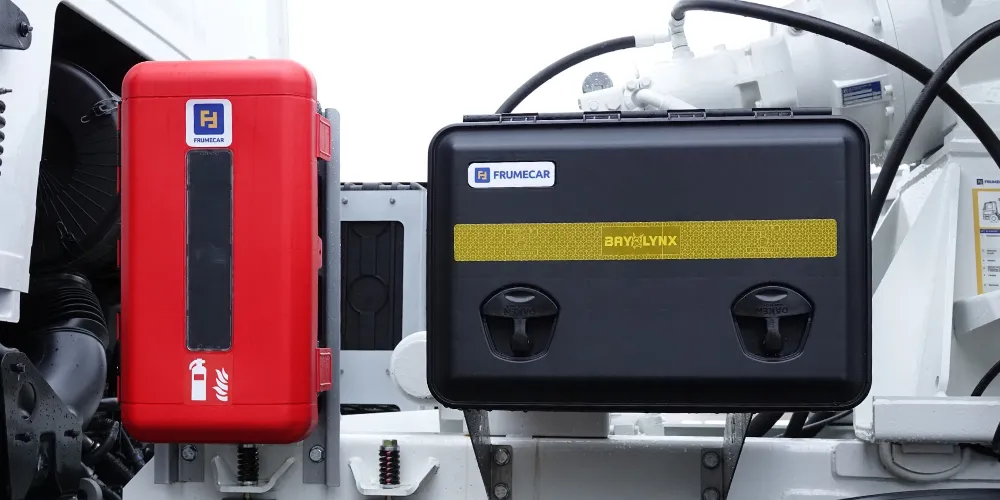
What Makes Frumecar Concrete Mixers Unique?
Built with high quality "HARDOX" grade steel
Lighter and thinner, harder and more resistant to wear than conventional steel.
Frumecar uses this type of panel in lighter concrete mixers thanks to its unique performance features; these will carry the HARDOX ® IN MY BODY logo, authorised by SSAB.
“PPG” wear-resistant paint
All of our concrete mixers have high-quality paint and protection made by PPG. These coatings provide the highest possible protection against wear caused by friction and exposure to the sun, extreme temperatures and other inclement weather. Frumecar is the only manufacturer of concrete mixers that uses this coating in our sector. Paint of this high quality is currently only used in the automotive industry.
Large hopper to optimise the loading process
Our high-capacity loading hoppers reduce the loading times, offering a more agile and effective system. We also prevent the jams caused by the accumulation of material in smaller hoppers, preventing potential faults.
Centralised greasing of the drum rollers
We all know the importance of greasing a machine like a concrete mixer, which has different elements that rotate relative to the position of fixed parts.
The ease of greasing from a single greasing point connected to all elements simplifies maintenance and facilitates optimum performance and maximum durability of the machine.
Cleaning the drum from the inside
It is of vital importance to ensure that the machine is clean at all times to guarantee a long working life of the concrete mixer.
Entering the drum to perform the cleaning tasks will increase the cleaning efficacy, while ensuring this task can be carried out easily and quickly.
Controls on the outside and cab
To start up the concrete mixer, simply press the control lever and button pad on the rear with the truck’s engine or auxiliary engine running.
These parameters have two control positions:
- Inside the cab: allows the operator to control the parameters from the driver seat, with a rotating control on one of the sides of the seat and a truck engine speed adjustment control next to the steering wheel.
- Outer control position: located on the rear, to the side of the truck driver cab, featuring a second rotating lever and button pad to control the truck engine’s RPMs.
Components from leading brands
All of our concrete mixers are manufactured using the components and materials of leading brands, which are known for supplying top-quality products.
We trust in leading tech partners for all of our components (SSAB, ZF, Eaton, Danfoss, …)
Our materials undergo a series of quality treatments and controls to ensure a top quality finish:
- Shot-blasting treatment and anti-rust primer applied before applying the final acrylic enamel finish.
- Joints sealed with silicone.
- Double polyamide epoxy primer coat with Zinc Phosphate on each component.
- Final finish on all parts with a double enamel coat, based on acrylic polyurethane resin, polymerised with aliphatic polyisocyanate.
- Dacromet® fastening elements.
The best equipped standard concrete mixers on the market
In addition to their quality, it is important to remember that Frumecar’s concrete mixers have the best standard equipment on the market.
They include a chute anti-wear lining, a 6mm reinforcement plate on the drum blades, a hand-trapping prevention system between chutes, two cases for fire extinguishers, a second water connection, auxiliary polyethene chutes, and plastic mudguards.
Request A Quote
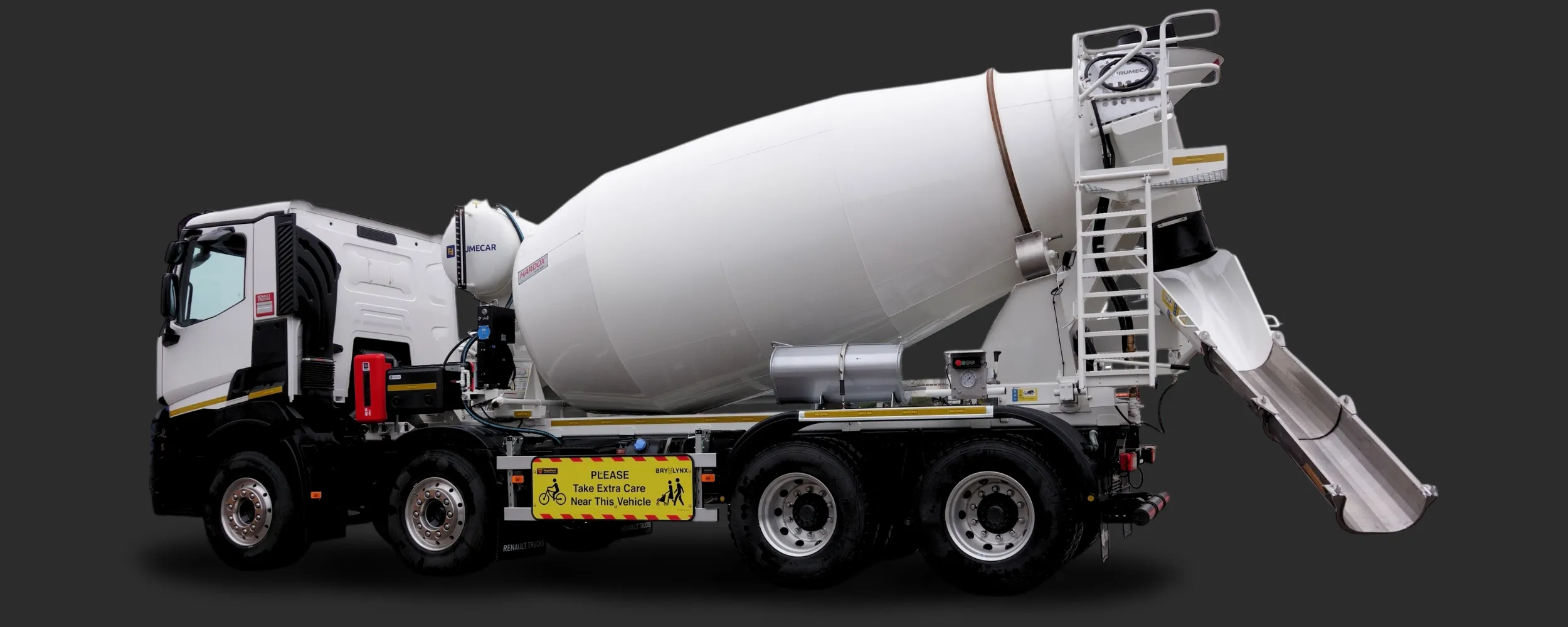